Three Equipment Component Duct Assumptions Prematurely Kill Airflow Efficiency
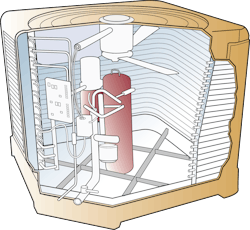
In the previous article, we looked at two duct system assumptions often made during equipment changeouts. These assumptions can create unseen liabilities for you as an installing contractor, but some consequences may not appear immediately.
For HVAC equipment to have a long, trouble-free life, airflow must be within manufacturer specifications during heating and cooling operations. Airflow often drops below acceptable levels if you attach air-handling equipment to undersized and restrictive duct systems. Unfortunately, there are consequences for this action.
Decreased airflow results in reduced equipment life and increased problems with comfort, efficiency, and maintenance. Restrictive duct systems are also harmful to three major system components. Let’s look at these components and how you can save them from premature death with simple diagnostic testing and repairs.
One: The Compressor
Compressors often suffer because of restrictive duct systems and low airflow. In cooling mode, compressor failures increase from refrigerant flood back and slugging. This consequence occurs because heat load on the coil decreases as airflow drops below an acceptable range.
Decreased airflow results in refrigerant boiling off much slower than required. Liquid refrigerant, instead of vapor, ends up back in the compressor, and you end up with oil washing off the compressor’s internal mechanical parts. In extreme conditions, this creates hydraulic action. Remember, a compressor is a vapor pump, not a liquid pump.
Most technicians will see clues of restrictive ducts and low airflow issues as they check superheat and subcooling. If you encounter low superheat and subcooling, remember to investigate the airside of the system. Don’t just assume it’s a bad thermostatic expansion valve (TEV). They react to the installation conditions, and a new valve will respond similarly.
Two: The Heat Exchanger
Heat exchangers also suffer from restrictive ducts and low airflow. This condition forces a furnace to operate outside of manufacturer specifications and creates a potentially severe risk to your customers.
When a furnace cannot remove the heat it generates, heat exchanger surfaces stress and weaken. Overheating causes the metal to expand beyond its normal range, resulting in joint separation and breaches. As you become more familiar with these failures, you will see that some heat exchanger styles fail more quickly than others.
Some clues of restrictive ducts and low airflow in heating mode include temperature rises exceeding nameplate ratings, primary limit cycling, and cracked collector boxes. Don’t assume the correct blower speed for a furnace is always low speed. The heating blower speed tap often needs to be the same as the cooling speed tap.
Three: Variable-Speed Motors
Restrictive ducts can also hurt electronically commutated motors (ECM) or variable-speed motors. Originally marketed as a solution for undersized duct systems, these motors are susceptible to damage like a compressor or heat exchanger, except not from low airflow.
A variable-speed motor adjusts to pressure changes in a duct system differently than its permeant split capacitor (PSC) cousin. A variable-speed motor moves the airflow it’s programmed for up to a specific limit. However, this ability comes at a price – the motor works harder and consumes more energy to achieve airflow.
Technicians often encounter these results when failed modules have overheated or become damaged by condensate. Another common complaint to be aware of is noisy system operation.
Uncovering the Cause
To uncover restrictive ducts and low airflow, it helps to measure static pressure. Why? Because static pressure is a necessary baseline test that gauges overall HVAC system health from the airside. You can spot many airside issues with a thorough visual inspection. However, static pressure measurements assign a value to what you observe.
Start with a total external static pressure (TESP) measurement. If it exceeds the manufacturer’s nameplate rating, you need to investigate further. TESP can tell you that a problem exists but can’t pinpoint it. You’ll need to perform additional pressure testing to uncover any airside restrictions. These measurements can help determine if the duct system is the culprit or if the issues are with the coil and/or filter.
Once you identify where the restriction is, you can suggest suitable repairs and solutions. Sometimes, it may be as simple as cleaning a coil or replacing an air filter. In other instances, the duct system will need additional duct capacity to reduce total external static pressure and increase airflow.
If you’re interested in a free quick-start guide for measuring static pressure, send me an email request, and I’ll be glad to get you started.
You Can Start Now
If you’re tired of frequent calls about these components failing, now is the time to find the real problems. Look beyond the equipment during the next service call where you encounter a failed compressor, heat exchanger, or variable-speed motor. Be sure to account for the duct system, or you might replace the same component again soon.
Don’t be surprised if more manufacturers require you to measure static pressure in the future as they seek to reduce their warranty claims and associated costs. They also want to prevent the premature death of the three components discussed here. The faster you begin measuring static pressure, the better.
With the updated SEER2 requirements and M1 testing standards, duct systems will be a focus for many manufacturers in the coming years. Why not be proactive instead of reactive?
David Richardson serves the HVAC industry as Director of Training for the National Comfort Institute, Inc. (NCI). NCI specializes in training that focuses on improving, measuring, and verifying HVAC and Building Performance.
If you’re an HVAC contractor or technician interested in doing duct upgrades correctly, contact David at ncilink.com/ContactMe or call 800-633-7058. NCI’s website www.nationalcomfortinstitute.com is full of free technical articles and downloads to help you improve your professionalism and strengthen your company.
About the Author
David Richardson
Director, technical curriculum
David Richardson serves the HVAC industry as director of technical curriculum at National Comfort Institute, Inc. (NCI), Avon, Ohio. NCI specializes in training that focuses on improving, measuring, and verifying HVAC and Building Performance.